

Environment
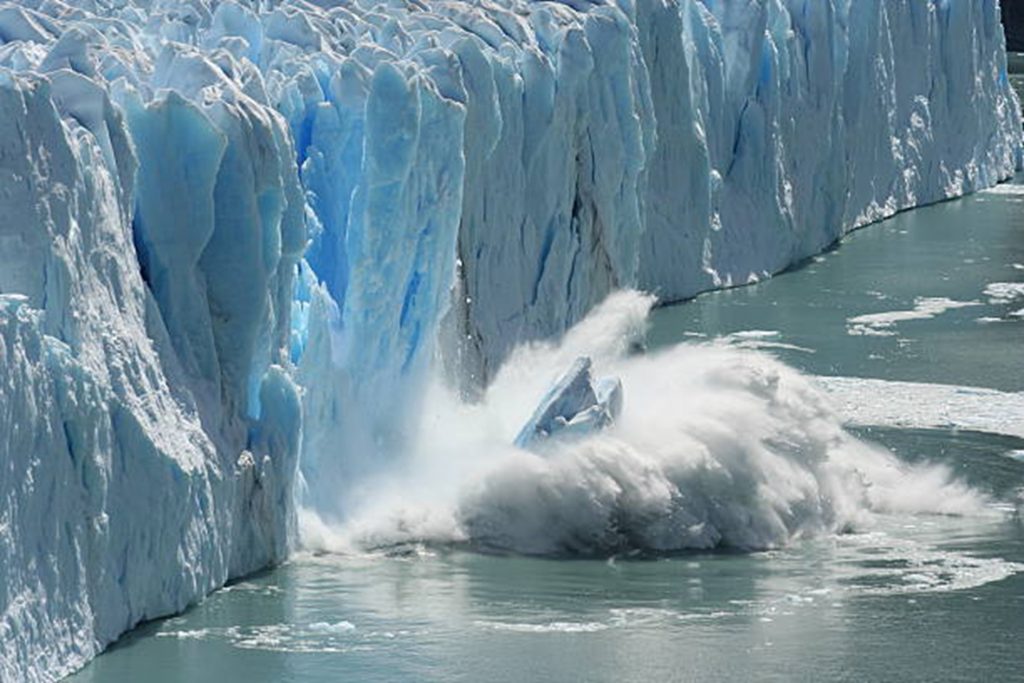
Climate protection, environmental awareness, sustainability – these issues concern us all.
How can I avoid wasting raw materials?
How do I create transparency from the procurement of raw materials to the finished product?
Can our company reduce greenhouse gases?
How do I make sustainability an integral part of the company philosophy?
That’s why we at Hydewa are always striving for improvements in product management and trying to break new ground in this regard.
All these questions have occupied us at Hydewa to try to do our part in the topic of sustainability commitment.
This begins with the purchase of raw materials. Since we source our main product, Glasbord®, from the United States, this requires prudent planning to avoid unnecessarily frequent transportation.
We also try to think “sustainably” when selecting our suppliers.
For example, for the lamination of our sandwich panels, we use ROMA5 BMB foam systems for the insulating core, in which biomass, which is obtained from organic kitchen waste, for example, is already used in production instead of fossil raw materials.
From our supplier ROMA, we thus receive a sustainable resource-saving PU foam system, in the production of which 50% of CO2 emissions can already be saved.
Another supplier Kingspan / EMS is distinguished by a “Certificate of Approval” BES 6001 (Certification for Responsible Procurement). This certificate includes and evaluates resource consumption, greenhouse gas emissions, energy management, waste prevention and management, traceability of materials, ecotoxicity and much more.
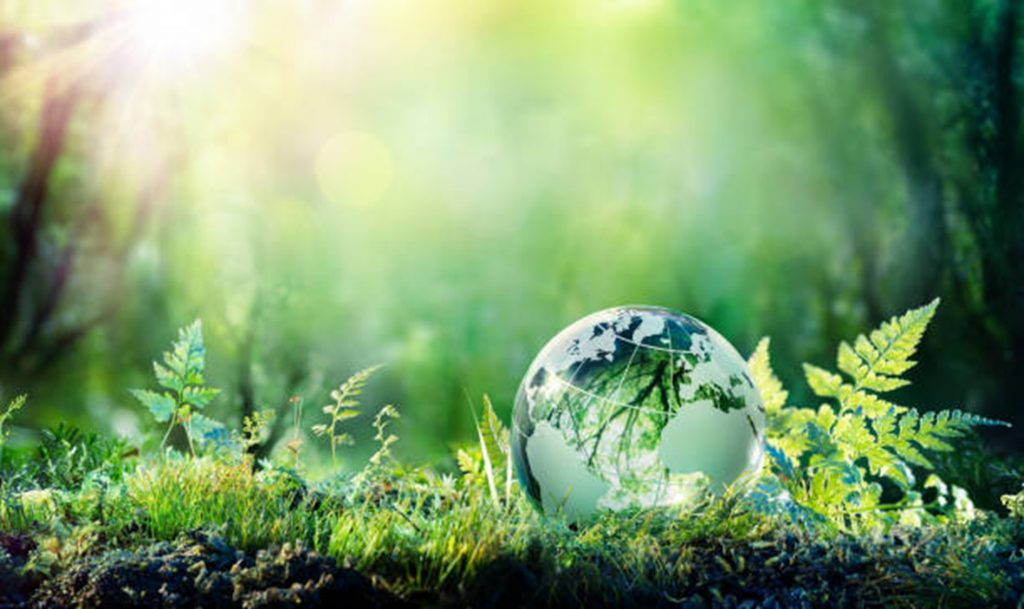
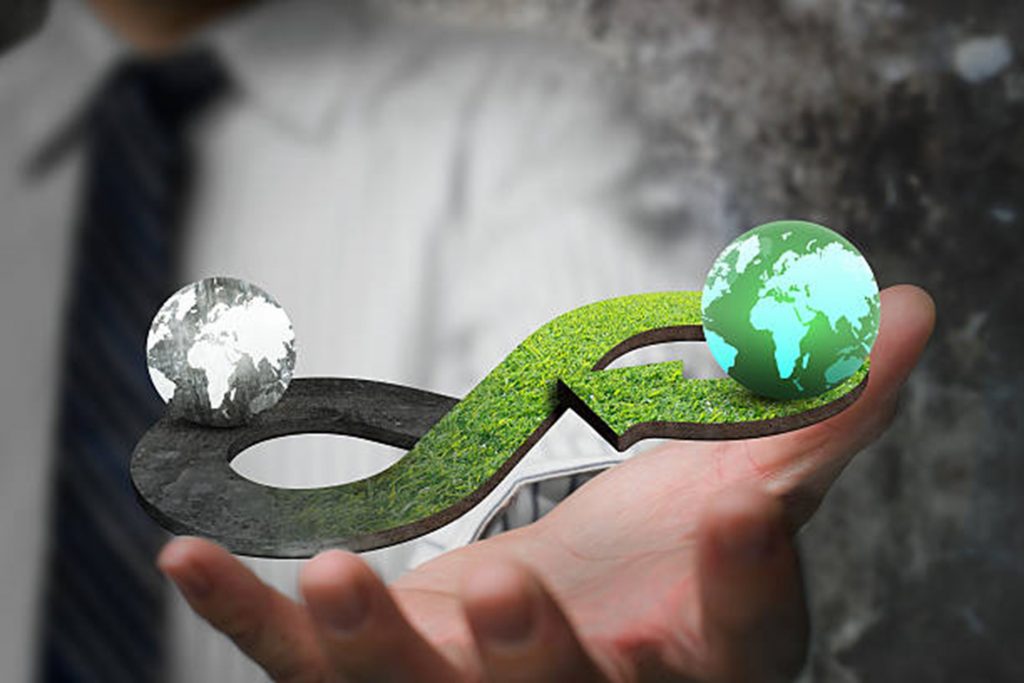
Packaging is very important for the protection and transportation of our products. At the same time, they also cause environmental pollution. Therefore, it is all the more important that our packaging material is recyclable or already comes from recycled material and is used as sparingly as possible. We use films that contain at least 25% environmentally friendly post-consumer recyclate (PCR) in accordance with DIN EN 14021 and can be returned to the recycling process after use.
Here again the circle closes, since in the area of production the primary goal is to avoid as much waste as possible. If this nevertheless occurs, we separate it and recycle it in the best possible way.
Important points are misproduction and reuse of B-goods.
Thanks to our quality management and constant further development, this percentage is very low.
Nevertheless, accumulating B-goods are structurally sound, but have “cosmetic” defects that do not meet customer specifications.
Meanwhile, we use these B-goods both internally in renovation and refurbishment projects, and also offer them, for example, as dust protection walls for construction sites, at cost price for collection.
Thus, each reused panel or sandwich element is one less piece on the waste pile and the internal renovation projects improve the working conditions of our employees in a cost-effective way.
The goal is to keep waste out of landfills and continue to increase the percentage of each material that is recycled in our current recycling streams.
Our recycling programs address specific materials such as metals, wood, plastics, chemicals and packaging materials.
All of our other waste from GRP, Styrofoam and plastics that cannot be sent for purely material recycling is collected in a 50 m³ roll-off container in cooperation with our selected, long-standing disposal company and processed into substitute fuel for the cement industry.
This disposal company has fixed quantity quotas or contracts with the cement plants, which is only possible if high-quality and monitored waste is delivered.
Styrofoam milling residues and GRP dust are compressed, collected in so-called big packs and also collected by the local disposal company.
Styrofoam residues that accumulate at the start of production, the end of production and coil changes are returned to the supplier and flow back into the product cycle.
Another environmental aspect is that we have short transport routes through the local disposal company, which also only supplies the regional cement plants.
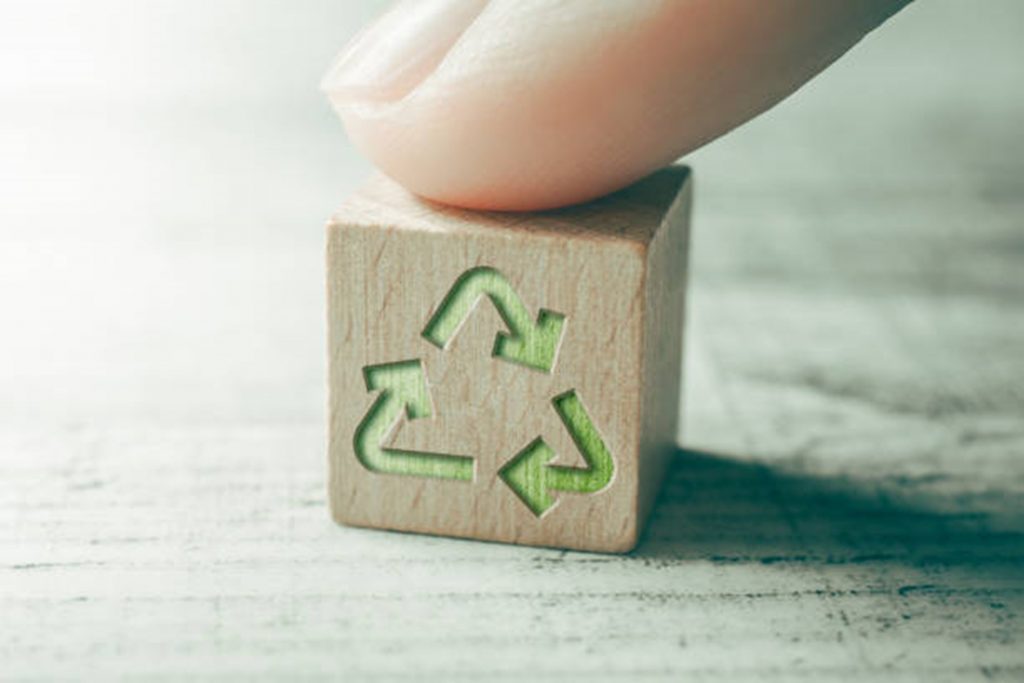
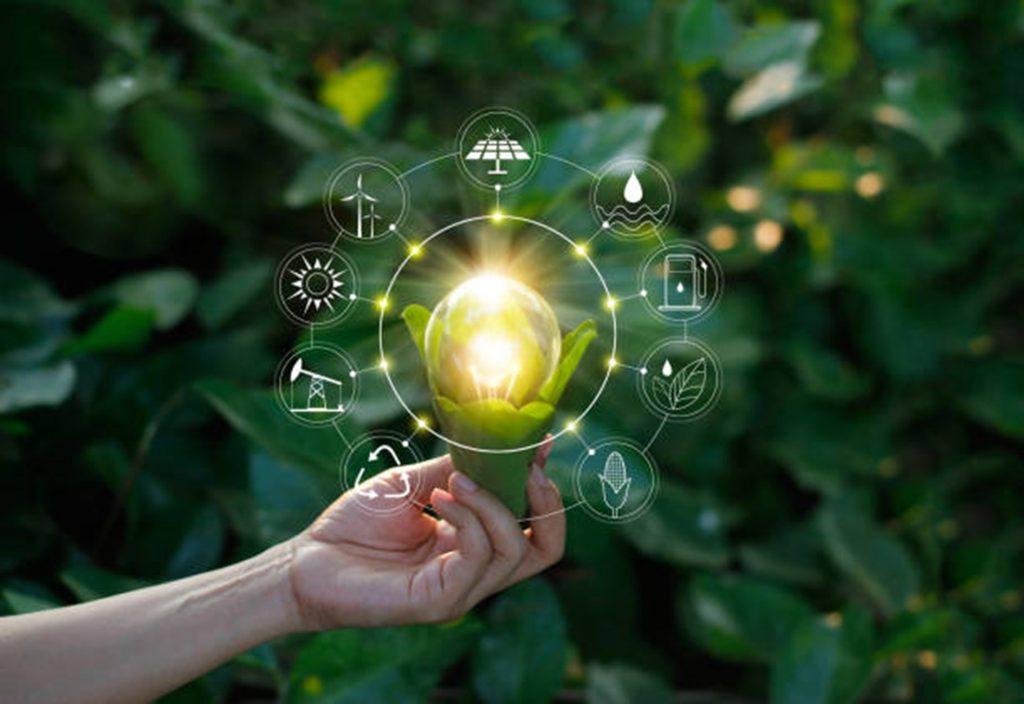
Energy and climate
Ultimately, we need energy to manufacture our products. The question is how much and where it comes from.
When it comes to the origin of our energy, we rely on photovoltaic systems and renewable energies by providing our employees with e-cars and charging stations on our company premises.
For a better energy balance, we have also equipped our office building with LED lighting, which impresses with its durability, low energy consumption and low heat generation.
We make a further contribution to the environment through the infrared hall heating installed in the warehouse.
This means concretely: up to 70% more energy saving and also less CO2 emissions.
As a responsible employer, we also rely on good employees and sensitize them to the topic of the environment.
And what could be better than to train them ourselves? Apprentices who can also be offered prospects after their apprenticeship in a family team.
Sustainability is also a team effort and does not just depend on the people in charge.
Only in this way can we pursue our goals and continuously improve.
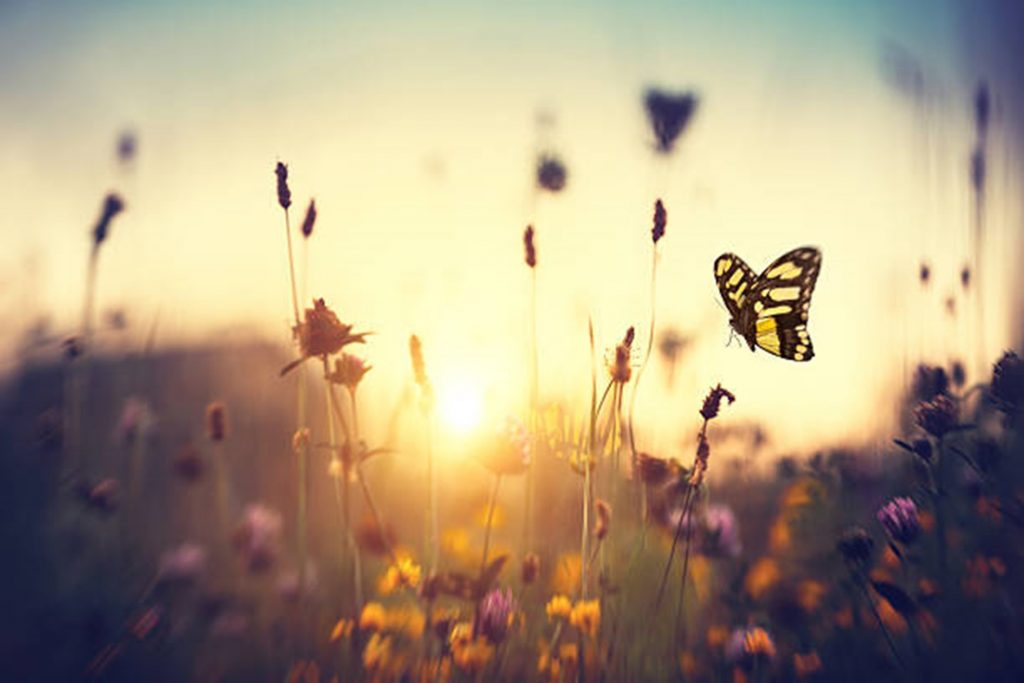